Let’s talk about shells in SOLIDWORKS Simulation. As a general rule, it’s good to consider using them if thin geometry is present. Yet we often see people stubbornly sticking with solid bodies, probably because there is less initial setup required. But when dealing with very thin parts, you might find yourself stretching both the resources of your system as well as your patience. Why? Because you need a ton of solid (tetrahedral) mesh elements to accurately capture thin geometry while avoiding highly distorted elements.
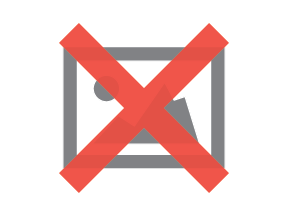
Model obtained from: http://www.3dcontentcentral.com/download-model.aspx?catalogid=171&id=12907
Lots of solid elements means many degrees of freedom, which means longer solve times and massive result data files (check out this previous post for more on that). Shells can be a life saver in such cases. They are finite elements with zero physical thickness. A special mathematical formulation allows for thickness to be taken into account – think of it as a “virtual thickness.” This makes shells a good choice for components that are very thin relative to their other dimensions (length, width, radius of curvature).
It’s good to keep in mind that shells are an idealization since zero physical thickness isn’t possible in the real world (maybe in some bizarre multiverse though)? Also, fair warning for the informed consumers among you: post-processing (everything you do once you have results) with shells can be a bit more complex than with solids. Whereas with solids you only have one stress value per node, with shells you have four: top, bottom, membrane and bending.
The good news is that in SOLIDWORKS Simulation 2015, shells are easier to work with than ever before. As many of you already undoubtedly know, there are three ways you can end up with a shell in a Simulation study:
a) A Surface Body in SOLIDWORKS – the simplest case.
b) Sheet metal in SOLIDWORKS – a slightly more complicated case where the sheet metal is a solid body in SOLIDWORKS, but its “sheet metal status” is recognized by Simulation and its midsurface gets automatically extracted and defined as a shell. Oh, and the sheet metal body’s thickness automatically gets applied to shell for you as well. Fancy!
c) A “manually” defined shell using the “Define shell on selected faces” functionality in Simulation – the case that tends to trip up users the most. We start with a solid body in the study, then select one or more faces of the solid to define a shell:
But how do we make sure the thickness is accurately represented? Check back next month for Part 2 of this post which will discuss shell alignment and offset!
Original Post Created by Jay Seaglar, Senior Simulation Guy at DS SOLIDWORKS
SUBMIT YOUR COMMENT