The word ‘precision’ is often confused with ‘accuracy’ and ‘resolution’ in describing a standard of exactness. In many engineering contexts, such as in 3D printing, ‘precision’ may refer to either accuracy of parts or the resolution of a machine.
‘Precision’ is also frequently employed as a more specific measure of repeatability in results: how consistently something can produce the same result. In the world of manufacturing, the word ‘precision’ can simply refer to the ability to produce parts that meet tolerances. Furthermore, the precision of a machine cannot be measured and quantified the same as the precision of the parts it yields.
So, how should we be thinking about and measuring precision in 3D printing? Here are three ways to define precision in 3D printing — plus factors that influence the precision of 3D printing, tradeoffs that come with certain definitions of precision, and considerations for choosing a 3D printer.
Defining precision in 3D printing As the word ‘precision’ can carry several different definitions, here are several different ways to define precision in 3D printing:
Repeatability of 3D printed parts: ‘precision’ here refers to a measure of variation in relation to repeatability. How consistently can a precision 3D printer produce the same result? Here, ‘precision’ is measured as how close measurements of the same part printed on the same machine are to each other.
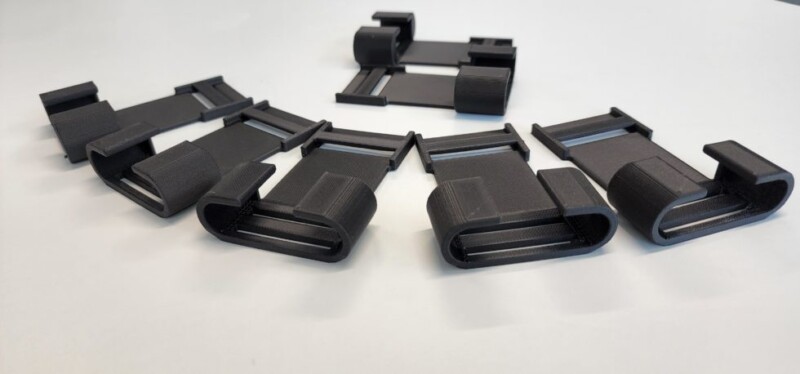
Dimensional accuracy and tolerance: However, from the more colloquial definition of ‘precision’ which means to be accurate and exact, the precision of 3D printed parts can also refer to the level of accuracy and detail that can be achieved in the printed object. How closely can the printed object match the intended design or dimensions of your digital file? Higher precision means the printed object is closer to the desired specifications.
One way to measure dimensional accuracy is through tolerance — which refers to the acceptable degree of variation or deviation from the intended dimensions or specifications of a printed object. It represents the allowable margin of error or the range within which the printed object can deviate from the intended design while still being considered acceptable.
Precision of a 3D printer machine: Another way to measure precision in 3D printing is through that of the machine itself. When discussing the precision of a machine itself rather than its output, the word isn’t so much a specific measure; rather a combination of the machine’s ability to print with accuracy, repeatability, and with high resolution: essentially, how exacting the machine can be in its ability to print parts.
Consider painting as an analogy — while throwing around a wide brush with fast, indiscriminate strokes is more efficient for covering area, a fine-tipped paint brush wielded by the hand of a trained artist can add a much higher level of detail.
Whether a 3D printer is broad or a fine-tipped brush largely depends on two variables of the 3D printer’s anatomy. A 3D printer includes 1.) a tool tip such as a nozzle, laser, or cutter; and 2.) a motion control system that maneuvers the tool tip across the axes.
If you are printing on two identical machines, but one with a nozzle size of 0.4mm wide, and one with a 0.25mm wide nozzle, the machine with a 0.25mm nozzle would be considered more precise. Given identical nozzle sizes, a machine with a motion control system that can operate in smaller increments of movement across the X, Y, and Z axes is considered more precise. For an overview of the role of 3D printing, read our article on how 3D printers work.
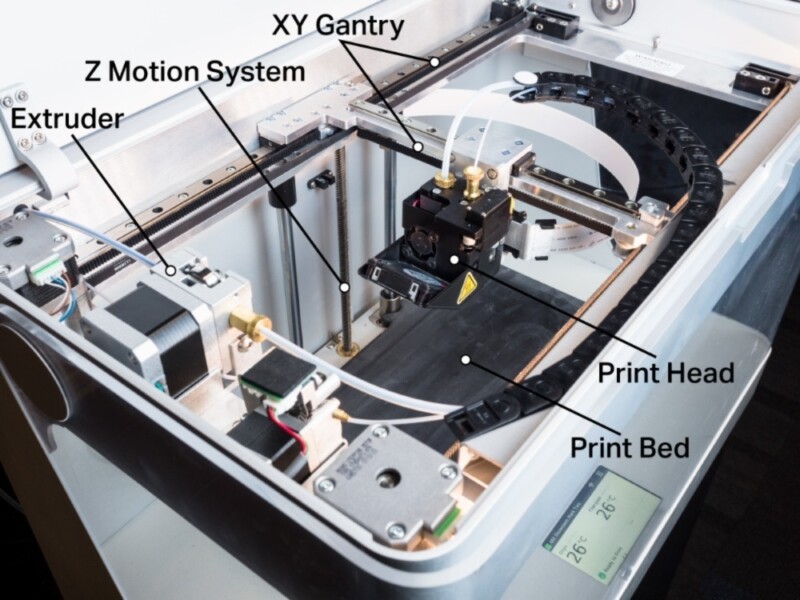
What factors can affect precision in 3D printing? Precision in 3D printing can be influenced by numerous factors, including:
Resolution: The resolution of the precision 3D printer determines the level of detail that can be achieved. It is often measured in terms of layer height or the minimum feature size the printer can reproduce. Smaller layer heights or minimum feature sizes generally result in higher precision.
Calibration: Proper calibration of the 3D printer is crucial for achieving precise prints. Calibration involves fine-tuning various parameters such as nozzle height, bed leveling, and extrusion rate to ensure accurate deposition of material.
Mechanical stability: The stability and rigidity of the 3D printer’s frame and components can affect precision. A well-built and sturdy printer is less likely to experience vibrations or wobbling during printing, resulting in more precise prints.
Material properties: Even though a printing process may be precise, the part output can be affected by material properties, such as shrinkage rates, thermal properties, and flow characteristics. Understanding and accounting for these properties can help achieve better part precision.
Design considerations: The design of the object being printed can also impact precision. Features such as overhangs, bridges, and intricate details may require additional support structures or specific printing techniques to maintain accuracy during the printing process, which may affect the accuracy of the printed part.
Post-processing: Many 3D printed parts require some amount of post-processing after the fabrication process, such as removal of support structures or sanding, which can affect the accuracy of the final part.
Tradeoffs for precision in 3D printing It’s important to note that achieving high precision in 3D printing may require tradeoffs.
For example, if machine capabilities are a controlled variable, printing with higher precision often requires a compromise in print speed. Using a smaller tool tip yields higher resolution prints; but as a result, material must be deposited at a slower rate.
Metal binder jetting, like on the Markforged PX100, is one exception to the general rule that precision inhibits speed, as this process can yield accurate parts very fast: by using multiple heads to simultaneously jet binding material in several different places at the same time. Therefore, a single build can yield tens or hundreds of accurate parts.
Precision 3D printing can also require new design considerations that weren’t previously taken into account, especially with complex designs. Fine or intricate features might need to be modified to ensure stability during the printing process.
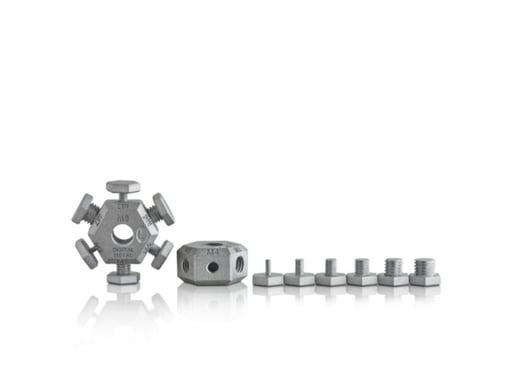
When thinking about 3D printing precision as repeatability of part accuracy, precision is of topical importance for any additive manufacturing application. Users should look for a reliable 3D printing platform with a track record of successful prints within the acceptable margin.
Considering tradeoffs in speed and material capabilities, the level of precision required for your 3D printer depends entirely on your organization’s specific applications in question. For example, while resin 3D printing is a great means for producing fine features, it will not yield parts quite as strong as high-performance industrial thermoplastics — which are a superior option for quickly producing strong tooling or fixtures.
For metal 3D printing, binder jetting is an excellent choice for precision without compromising speed. It can produce accurate parts quickly with repeatability while using less energy (therefore lowering operating costs per part) — which makes platforms such as the Markforged PX100 a strong option for precise metal production at scale.
To read the full article, click here.
Click here to learn more, get a quote, or contact an expert at The SolidExperts.
SUBMIT YOUR COMMENT