Matthew Wolak had a problem: He loved the freedom of driving his 2016 Jeep Wrangler with the roof panels and doors removed. But the large plastic screws that hold the roof panels in place were an ergonomic nightmare to remove and install.
As a former salesperson for GSC, a Milwaukee-area Markforged distributor, Matthew decided to do something about it: He designed and 3D printed two types of tools out of Onyx – a hand-crank model and one that’s designed to fit on a power drill – to make this process faster and easier. He’s now selling them to other passionate adventurers who are also frustrated with this shortcoming.
Here’s a closer look at his entrepreneurial story.
A major pain point
As a Jeep owner, what was the pain point that made you decide to create these rooftop panel removal tools? This issue affects Jeep Wranglers built between 2007 and 2019. To take off the roof panels, you must remove two large plastic screws. They’re about 4 inches in diameter and are located just behind the front seats, near the dome light. To reach them, you must lean back and then rotate them by hand. Their awkward location and size cause you to clench your hand and rotate your wrist in a way that puts a lot of stress on them. It’s not ergonomically designed for the human hand.
What was the trigger that made you say, “That’s it. I can’t stand it anymore. There’s gotta be a better way”? It was my low threshold for patience with all things mechanical *laughs*. I just wanted something to make it easier because there’s nothing better than riding in a Jeep with the top and the doors off. It’s part of the Jeep mystique. It’s awesome!
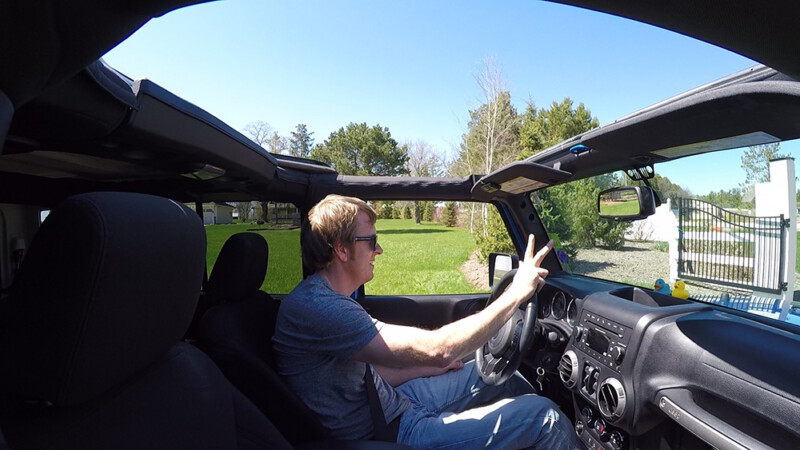
Designing a solution
Would you say you’re a problem solver? Yes, definitely. My brain is wired in such a way that it’s always looking for ways to improve everything. I spent the first half of my career as an advisor for Solidworks, a popular CAD tool.
During the last several years, I sold the Markforged Digital Forge for a distributor. I visited many factories, helping workers replace their improvised manufacturing aids with tough-as-nails fixtures and work-holding tools that were precision-made using Onyx.
Those two skill sets convinced me that I could design and 3D print a tool that would solve this frustrating and time-consuming problem.
Which tool came first? The drill-mount tool or the hand-crank model? The hand-crank version was the only one I was planning to design. But after many failed designs, the light bulb went on. People had been suggesting to me that I make a drill driver version. One day, after much frustration, I realized that I had already designed the part of the tool that mates with the rooftop removal screws. All I needed to do was modify it slightly to receive a chuck adapter for a power drill. Boom – it was done and it worked fantastic!
By comparison, the design of the hand-crank tool was a painstaking process. It took about a year and 19 iterations to perfect it. I spent many early Saturday mornings with my friend and former colleague, Fred Bohlmann. His expert-level CAD skills helped me develop the optimum design for it.
When you were designing the hand-crank tool, what were some of the challenges you faced? One of the biggest problems was that you needed to put upward pressure on the tool to keep it engaged with the rooftop removal screws. That was very awkward. So we designed the head of the tool with teeth around its outside perimeter so it could grip the screws. But when you attached the tool to the screw, those teeth needed to flex. That kept them from snapping off.
Once we solved that problem, it was much easier to turn the crank and the screws would come right out, with much less effort.
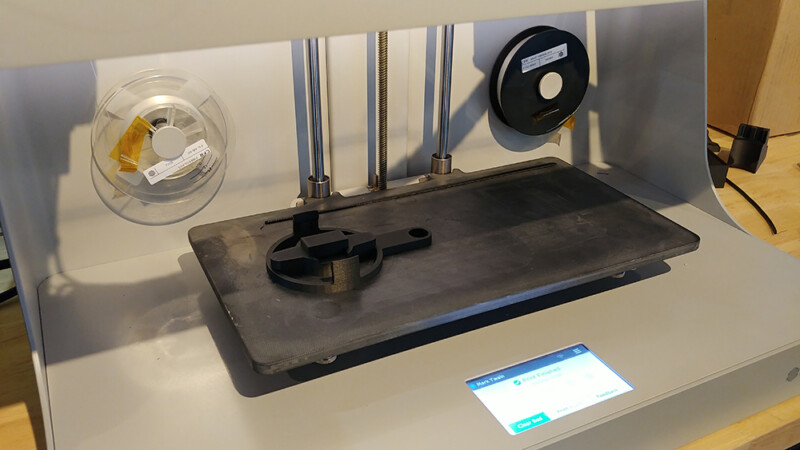
Spinning up a solution with Markforged
Which printers are you using to produce these tools? They have always been made on either an Onyx One or Mark Two.
Because the tools you designed are used by consumers, was a high-quality surface finish a key requirement for these tools? It definitely was. I wanted to build something with a high-quality look to it. People want to feel confident in what they’re buying. If it looks nice, that’s half the battle. The tools printed in Onyx are tough and they also look great!
When did you start selling these tools and what has the response been from Jeep Wrangler owners? I started selling them at regional Jeep events in February 2022. They sold well at every show we attended. It’s been a lot of fun to see the response to them. When people see them in action, they want one! Based on that amazing level of response, we recently started selling them online.
Do you think the Markforged product line empowers entrepreneurs to bring ideas like yours to life using additive manufacturing? Absolutely. When you have the confidence to know you can 3D print something as strong as aluminum, it opens doors to builds that have never been possible.
To read the full article, click here.
Click here to learn more, get a quote, or contact an expert at The SolidExperts.
SUBMIT YOUR COMMENT