Metal X Spotlight: A Competitive Advantage for Electric Vehicle Busbar Prototypes
While internal combustion engines still fuel the majority of today’s cars, electric vehicles (EVs) will have a major role shaping the future of transportation and automotive. Research shows that EV sales have leaped over 40% a year since 2016, with EVs projected to be the largest market in the automotive sector in the next 10-15 years.
Despite the industry’s growth, automotive providers still struggle to achieve profitability on EVs sold due to manufacturing challenges: many components for EVs are complex and difficult to manufacture efficiently. Just like vehicles powered by fossil fuels, entire supply chains are being built around electric vehicles. As Tier 1,2, and 3 automotive suppliers scramble to win business in this market, their competitive advantages will be cost savings, time to market, and design optimization.
To build tighter and more efficient supply chains wherever possible, automotive manufacturers must examine every area of opportunity. One opportunity is 3D printing electrical components, such as busbars, with pure Copper on the Metal X system. In this article we will explore how prototyping these components enables companies to accelerate time to market, while realizing areas for cost reduction and design optimization.
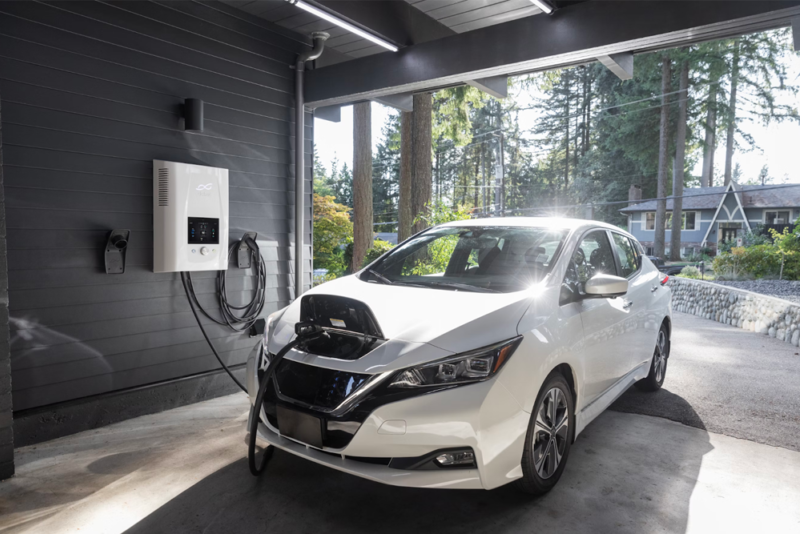
Busbar designs: complex but important
A busbar is an electroconductive metallic bar that distributes current to subsystems in intensive electrical applications, such as electric vehicles. In EVs, a well-designed busbar is a critical component for efficient power distribution across the vehicle. Designing the right busbar can be complex, however—engineers must work with multiple constraints. The right busbar design is important for achieving optimal electrical performance, but requires you to work within the boundaries of both form factor constraints and heat dissipation requirements.
Busbars in electric vehicles are often made of pure Copper, due to the material’s high electrical conductivity. Pure copper has excellent electrical properties, but is a difficult material to work with in traditional manufacturing: which means high price tags and long lead times.
Using today’s technology for a competitive advantage
Working within the additive manufacturing industry, I am firsthand witnessing the struggles that automotive suppliers are facing to quickly and cheaply prototype Copper parts. These components are critical, and it is exciting to realize that our technology can help alleviate these challenges. Considering the busbar’s performance demands are within the capabilities of metal 3D printing today, it’s a pretty perfect candidate for a strong, high-value additive application.
Typically, getting a busbar prototype in hand through traditional manufacturing processes will cost somewhere around $200 per iteration, with a lead time of around three weeks. While it typically takes a series of iterations to arrive at an optimized part, it’s common for high costs and long lead times to force a compromise in the number of iterations designers can go through. The need to meet tight deadlines may mean that a truly optimized part may not be realized.
The ability to 3D print in pure Copper to prototype busbar designs offers electric vehicle suppliers several competitive advantages: reducing cost on each iteration, avoiding long lead times due to bottlenecks in machining centers, and empowering engineers to rapid prototype on experimental designs. Printing a busbar prototype with the Metal X System in pure Copper would typically cost around only $55 with a lead time of just three days. The Metal X can turn around nine iterations in the same time it takes to get just a single iteration through traditional fabrication—allowing engineers to test designs in real-world conditions with time that would otherwise be spent waiting for parts to arrive.
Our Metal X system makes it faster, cheaper, and easier than ever to rapidly prototype with electroconductive materials. It’s the first metal 3D printer that is capable of printing pure Copper parts. Alternative metal AM technologies can print only Copper alloys; since production busbars must be made of pure Copper, prototyping alloys will not yield the same performance insights needed for the production part.
The Metal X system is a powerful tool in the toolbox for designers, engineers, and technicians to address a broad range of both prototyping and production challenges. If you’re looking to 3D print industrial prototypes, tools, spare parts, or end-use parts, reach out to our team to help you evaluate if the Metal X is a fit for your organization’s manufacturing needs.
To read the full article, click here.
Click here to learn more, get a quote, or contact an expert at The SolidExperts.
SUBMIT YOUR COMMENT