The ABCs of 3D Printing
What do a house, a coral reef, skin cells, and a cutting saw have in common?
They all have been 3D printed.
It’s no secret that 3D printing is accelerating innovation in numerous industries, including dentistry, eyewear, prosthetics, furniture design, archaeology, paleontology, and forensic sciences. And we’re just getting started with realizing the full potential of 3D printing on drastically improving the way we live and work.
What Is 3D Printing?
3D printing can take the form of many different processes in which a part is additively created by introducing or bonding additional material. 3D printed objects can be geometrically complex and are ideal in a wide variety of manufacturing applications. Machines can cost anywhere from hundreds to millions of dollars and use a wide variety of technologies to print parts.
3D printing is a subset of additive manufacturing. Additive manufacturing is where a part is made by adding material, whereas the subtractive manufacturing process is where a part is made by subtracting material. In 3D printing, a 3D printer makes a three-dimensional object by starting from a CAD (computer-aided design) file. There are a variety of materials and 3D printing technologies available, making it easier than ever to create parts for all sorts of industries.
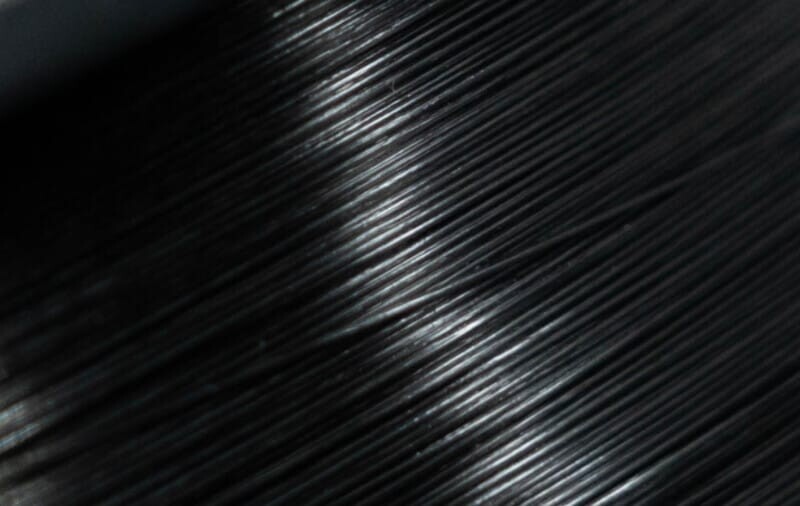
How Is 3D Printing Used in Manufacturing?
While 3D printing has often been linked to toys and hobbyist items, they are more than capable of producing parts that can withstand a multitude of heavy-duty environments. You can find 3D printed parts being used in manufacturing processes in industries such as energy, automotive, and defense. From functional prototypes, tools and fixtures to end-use parts, the 3D printing industry is transforming many other industries and processes.
Most people assume 3D printers are a new technology, though you may be surprised to know they’ve been around since the 1980s. However, printers up until 2009 were mostly used for industrial purposes and were prohibitively expensive to use for most companies. Nowadays, businesses around the world use 3D printers to build parts for manufacturing purposes with significant improvements to 3D printing costs. Much of the growth in the 3D printing industry comes from an explosion in using 3D printing in manufacturing, something previously thought impossible when the process caught on.
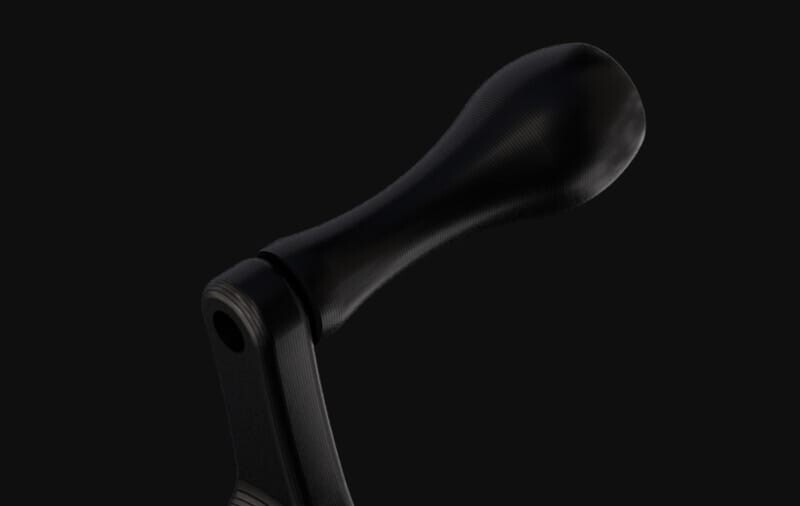
What Are the Most Common 3D Printing Technologies?
While there are many 3D printing techniques, let’s focus on a couple of common types. All printing technologies build parts in discrete slices called layers.
- Fused Filament Fabrication (FFF, also known as Fused Deposition Modeling)
- Continuous Fiber Reinforcement (CFR)
FFF (Fused Filament Fabrication)
Fused filament fabrication is the most common and affordable type of printing, and most machines use this technology. In FFF, the printer heats up thermoplastic to a near-melting point and extrudes it out a nozzle that traces the cross section of a part for each layer. This process repeats for each layer.
Continuous Fiber Reinforcement (CFR)
Continuous fiber reinforcement is a process that enables 3D printers to reinforce FFF parts with continuous fibers. A CFR-capable machine uses two extrusion systems—one for conventional FFF filament and a second for long-strand continuous fibers. Continuous fibers are laid down in-layer, replacing FFF infill. The resulting parts are significantly stronger (up to 10 times stronger than any standard FFF material such as ABS or PLA) and can replace aluminum parts in-application.
Today, fused filament fabrication 3D printers are the more widely used 3D printing technology. However, carbon fiber reinforced materials deliver on the benefits of FFF by eliminating key part weaknesses. While FFF parts are typically limited by the strength of weak polymers, CFR parts are strong enough to replace machined aluminum in key manufacturing operations.
To read the full article, click here.
To learn more about 3D Printing, contact an expert at The SolidExperts.
SUBMIT YOUR COMMENT